平成17年12月8日 集談会口演
飛沫感染防護簡易アイソレーター試作のための技術的検討
成田空港検疫所 菊池 均
(スライド1)
はじめに
●現有のトランジットアイソレーターは1台で、使用後消毒終了までの空白期間が生じる。
●現在の市販品には価格、機能、重量などの不満がある。
●安価で軽量で取り扱い容易なものが望まれる。
●飛沫の飛散距離は1〜2m。患者との間にビニールカーテンをおく事で飛沫感染防止が可能である。
●救急車にガムテープでビニールシートを固定する方法は、確実な設置が困難であった。
|
現在成田空港検疫所には、感染症患者搬送用のトランジットアイソレーターが1台配備されている。しかし予備機はないため、1度使用すると消毒終了までの間使用できず、この間に患者が発生した場合には感染防護を行うことができない。検疫所で感染症患者を搬送する事例が発生する頻度は非常に低いが、搬送が必要になるときには患者が集団発生する可能性もあり、予備のアイソレーターの配備が望まれた。しかし現在市販されているアイソレーターは価格、機能、重量などの面で不満がある。特に感染症対策の基本である使い捨てを実現するには高価である。
一方感染経路の中心は飛沫である。飛沫感染感染症は飛沫による感染のみと考えられており、また空気感染(飛沫核感染)においても、その感染の中心は飛沫であると考えられる。この飛沫を防御するには、患者の周囲にビニールシート1枚置くことで飛沫を防ぐことができる。この考えから、救急車にビニールテントをガムテープで設置する方法があるが、当所の保有する救急車には、内装の問題のため適用することができなかった。
(スライド2)
目的
|
●飛沫感染防護に限定した簡易トランジットアイソレーターをDIYで試作する。
●基本形状は右図に示すビニールテント型とする。
●当所の機材に適合し、軽量安価な物の試作を目標にする。
●試作と評価を反復し現場に適した形状を検討する。
●試作に必要な技術と手技を確立する。
|
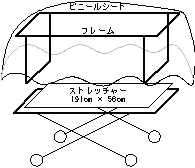 |
そこで、飛沫感染防護機能に割り切った簡易トランジットアイソレーターの作成を試みた。基本形状を図1に示す。ストレッチャーの上に直方体のフレームを乗せ、この上にビニールシートをかぶせる形とした。さらに当所の保有するストレッチャーに容易に設置できる形状で、軽量で安価でかつ使いやすいものを試作することを目標とした。このため試作と評価を反復し、現場に適した形状を検討した。
フレーム材料の検討
|
軟鉄: 曲げ、切断、接着容易。安価。錆びる。
ステンレス: 堅く、加工が困難。
アルミニウム: 一度曲がると強度が落ちる
木材: 横からの力で折れる。
∴ 軟鉄を選択
丸棒: 自由な方向に曲げることが可能。
パイプ: 重量の割に強度がある。曲げなどの加工が困難。
∴ 6mm軟鉄丸棒を選択した。
|
まずフレーム材料の選択を検討した。軟鉄は、髷、切断、接着などの加工に種々の方法があり、かつ安価であった。欠点として錆びることがあげられた。ステンレスは素材が堅く加工が難しいこと、アルミニウムは軽量であるが一度曲がると強度が落ちること、木材やプラスチックは横からの力で折れる問題があった。以上より軟鉄を選択した。次に形状として丸棒とパイプがあるが、パイプは重量の割に強度があり多用されるが、曲げ加工が困難な事、切断した断端が鋭利になるため受傷の危険がある。このため丸棒を選択した。
軟鉄丸棒を6mm,9mm, 12mmの丸棒を比較したところ、最も細い6mm軟鉄丸棒でビニールテントのフレームとして充分な強度が得られることが判明したため6mm軟鉄丸棒を使用することにした。
加工方法
|
切断: ディスクグラインダー
曲げ: 曲げ治具を自作
接着: アーク溶接、 リベッティング
溶接: 家庭用アーク溶接機を使用。
家庭用電源(100V15A)で使用可能。
専用の低電圧溶接棒を使用する。
厚さ2〜3mmの平板、9mm程度の丸棒の溶接が可能。
リベッティング: 針金を通し両端をつぶす。
板厚+(穴の直径×2) の長さの針金を使う。
1カ所を固定すると回転が可能。今回ジョイントに使用した。
2カ所を固定すると、回転しない接合が可能。
|
加工方法については、切断はディスクグラインダーを使用した。なおジグソーも使用可能である。曲げは、曲げ治具を自作した。接着はアーク溶接とリベッティングを使用した。
溶接は家庭用アーク溶接機(交流)を家庭用電源(100V15A)で使用した。この溶接機により平板2〜3mm程度、丸棒6〜12mmφ程度の溶接が可能であった。
リベッティングは、2枚の板に貫通する穴をあけ、この穴に板厚さ+穴の直径×2程度の長さの針金を通し両端をハンマーでつぶして固定する。1カ所を固定すると回転する接合が可能であり、今回ジョイントとして使用した。2箇所以上を固定すると回転しない接合が可能である。
ボルトとナットを使用する方法は、分解可能なメリットがあるが、ボルトの突出部が受傷の原因になること、ゆるみやすいこと、ナットが脱落すると崩壊し機能を失うことなどのため使用を避けた。
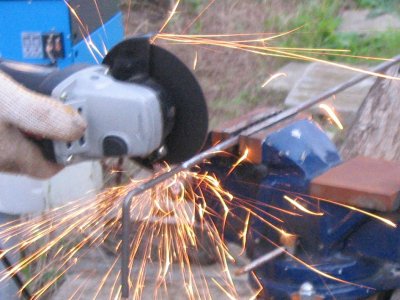
ディスクグラインダーに切断砥石を装着して材料を切断しているところを示す。写真にしめすとおり大量の火花を散らしながら切断が行われる。切断後は断面が鋭利になるため切削砥石による断端処理を行う。
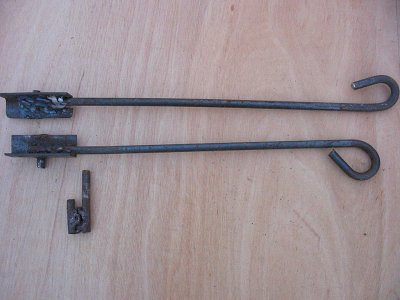
次に曲げ治具を示す。固定治具(下)はJ字型で、下部を万力で固定する。曲げ治具(上、中)は写真からはわかりにくいがJ字型の固定治具を通す穴がある。曲げ治具の使用方法を図で示す。固定治具を万力で固定する。それをま上からみたものが左下図である。ここに材料を置き、曲げ治具の穴に固定治具の棒を通し、曲げ治具の縦棒をひっかける。この状態で曲げ治具を固定治具の軸を中心に回転すると右上図のように一定の半径(この治具では内径4.5mm)での曲げを容易に行うことができる。
次にリベッティングを示す。左上の図に示すとおり2枚の平板を貫通する穴を開け、これに針金を通し、下を浮かせた状態で針金をハンマーで垂直に軽くたたくと次第に両端がつぶれ、左下図のとおり2枚の板を強固に接合することができる。今回は右図の形状で、使用した針金は#12(2.6mmφ)を使用した。なお市販されているリベットは多くがアルミ製のため、ジョイントをフレームに溶接する際に溶融する可能性がある。
アーク溶接
|
溶接棒と母材の間でアーク放電を起こし、溶接棒と母材を溶かして接着する。
溶接時に発生する紫外線と高熱のため、保護面や保護手袋を着用。自動遮光面が有用。
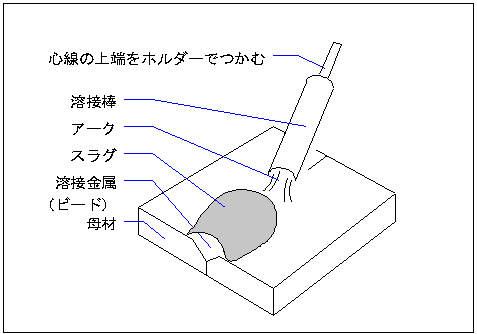 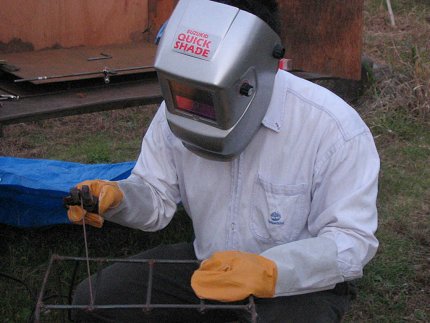
|
次にアーク溶接を示す。アーク溶接は、溶接棒と母材の間でアーク放電を起こし、溶接棒と母材の両者を融解し接着する。溶接の特徴として、任意の場所で任意の角度で強固な結合を得ることが可能である。断端どおしの接着も可能であった。一カ所あたり溶接の時間は30秒〜1分程度で、費用は25円程度であった。溶接作業の際には溶接時に発生する紫外線と高熱からの防護のため、保護面や保護手袋を使用する。保護面は自動遮光面が有用であった。
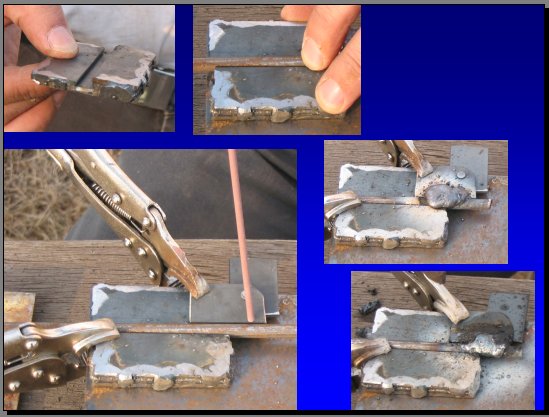
また、溶接は任意の位置で接着が可能なため、溶接前に母材を希望する位置・角度に仮固定してから溶接を開始する必要がある。このため随時治具を製作しながら作業を行った。図に6mm丸棒と3mm厚平板を高さをそろえて固定するために製作した治具を示す。溝の部分に丸棒を置きバイスクリップで固定し、次に平板(この場合は作成したジョイント)を置きバイスクリップで固定し、溶接を行う。溶接後の状態と、表面のスラッグを除去した状態を示す。
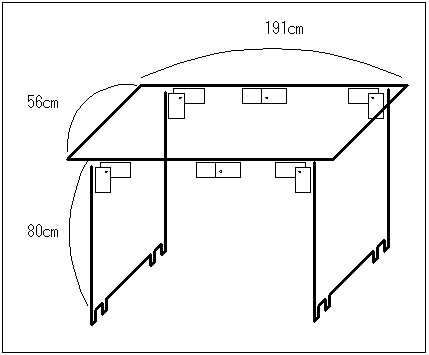
このような手技を使用し作成したフレームを示す。写真は試作5号機である。非使用時の小型化のためジョイントを6カ所設け、足と胴体中央部が折れるようにした。曲げ加工で作成しているためフレームの角が丸く受傷しにくいと考えられた。
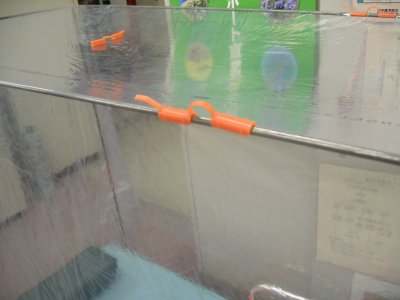
これにビニールをかぶせた。ビニールの固定にはプラスチック金具(シャクトリムシ(R))を使用したところビニールを破かず強固に固定することができ、今回の目的に適合した。またフレームにビニールをかぶせ、ビニールを張って固定することでフレームの補強になり安定した。
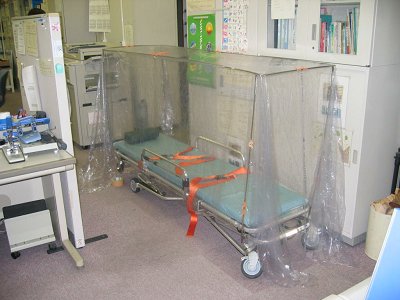
試作1号機をストレッチャー上に設置しビニールを固定したところを示す。
まとめ
|
DIY技術を適用することで、製作を外部委託せずに試作品の自作が可能であった。
安価(材料費約2000円)、軽量(約2.5kg)を実現した。
手技の修得には試行錯誤と反復練習を要した。
DIYのため試作と検証の繰り返しが可能で、現場の要求に適した試作品を作成することが可能であった。また試作品を実用に供することも可能と考えられた。
今回の手技は、アイソレーター以外に診察用飛沫防護スクリーンの試作などに応用が可能であった。
|
以上をまとめる。
DIY技術を適用することで、製作を外部委託せずに試作品の自作が可能であった。 材料費約2,000円、重量約2.5kgと、廉価で軽量を実現した。
DIYによるプロトタイピング試作により、現場で必要とする機能を満たす市販品が存在しない際に、試作品を用いて機能を検討することが可能であった。
DIYによるプロトタイピングは本来試作品であり、本来実使用には安定した加工品質のため鉄工所に発注することが望ましいが、今回使用した手技では実用強度が得られ、試作品を直接使用することも可能であると考えられた。
手技の習得、特に安定した溶接の習得には試行錯誤と反復練習を要した。
職員自ら製作したため試作と検証の繰り返しが可能であり、現場の要求に適した試作品を作成することが可能であった。